What is the true value of data?
More effective vessel operations can be organized into four steps. Learn how to make better use of data within this framework.
Keywords: digitalization, shipping, BlueBox, value, performance
One of the most common mistakes in the implementation of digitalization is believing that data will solve all the problems. Data, alone, has no value. The true value of data is extracted when it is analysed, interpreted and corrective actions are implemented. And field expertise is an essential part of interpreting results and suggesting improvement actions. Ulstein, as builder and designer, has the expertise to support you on your digital journey.
Understanding the value of data
What is the value of data? Ackoff (1989) suggests that “data, like metallic ores, are of no value until they are processed into a useable (i.e. relevant) form”. As Ackoff points outs, the millions of data records being generated onboard vessels are of no value if they are not given specific use. Of course, many of them have already a purpose onboard the vessel. Eg. measure the oil temperature of an engine and triggering an alarm if the value exceeds a threshold. However, the value of those data signals can be further enhanced or augmented by exploring other complementary interpretations and uses. Why should not oil temperature be used to predict malfunctions in the engine, or planned maintenance activities?
The more we process data (not data manipulation), the higher its value becomes. Information normally reflects the contextualization of data. Data monitoring and reporting are sources of information. They support decision-makers to answer questions such as where a vessel is operating. How much fuel has been used? What kind of cargo is it carrying?
Understanding how to increase the effectiveness of vessel operations requires, however, knowledge. Knowledge results from extracting meaning from information, which requires complementary field expertise. Expertise in vessel design and vessel operations is essential to interpret data and information from vessel operations and to identify and propose areas for improvement.
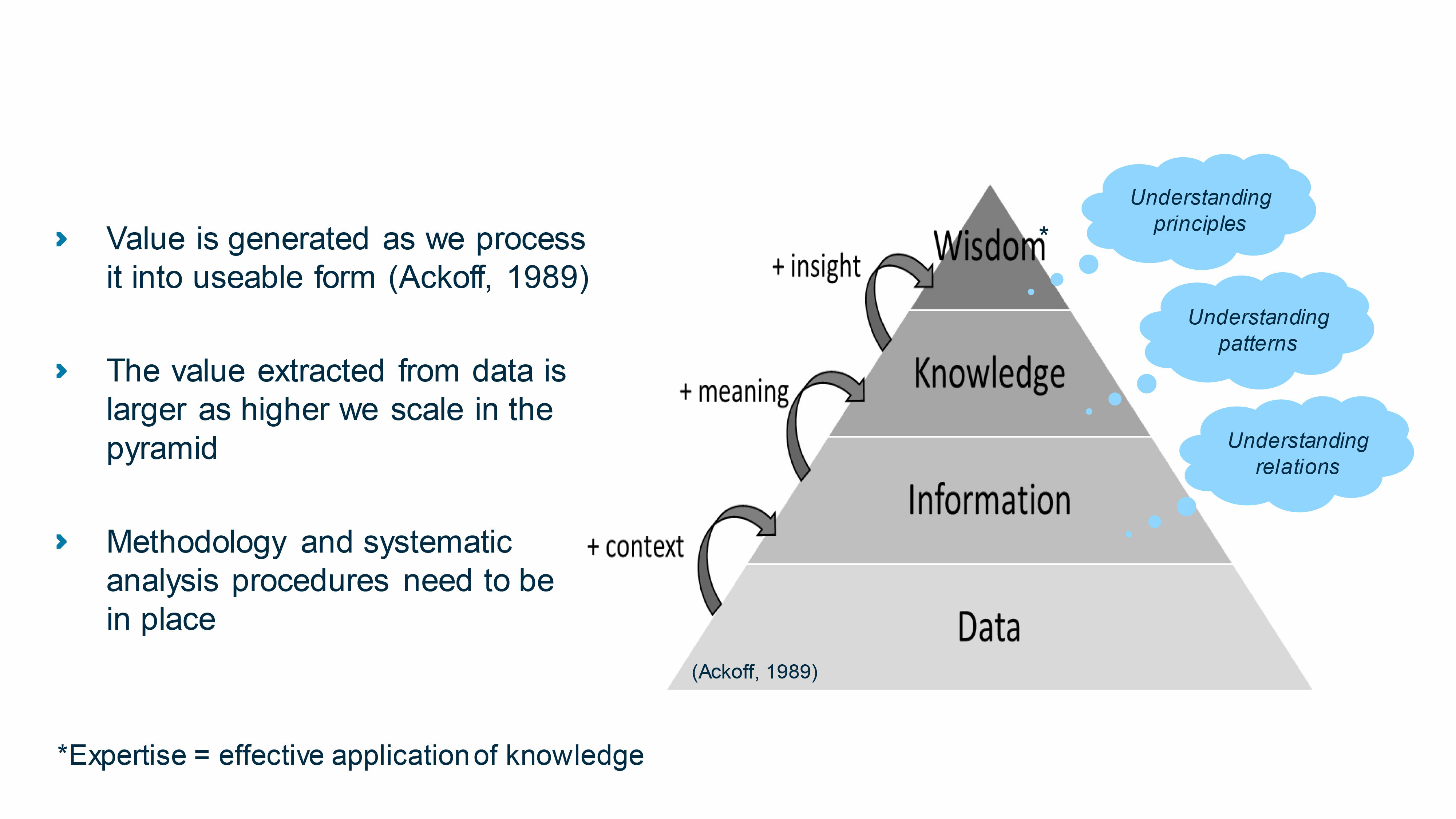
Four digitalization steps towards value creation
Ulstein has developed a four-step digitalization approach to gradually extract and interpret value from data. The implementation of the services can be carried out stepwise (start with Step 1 and continue as demand requires).
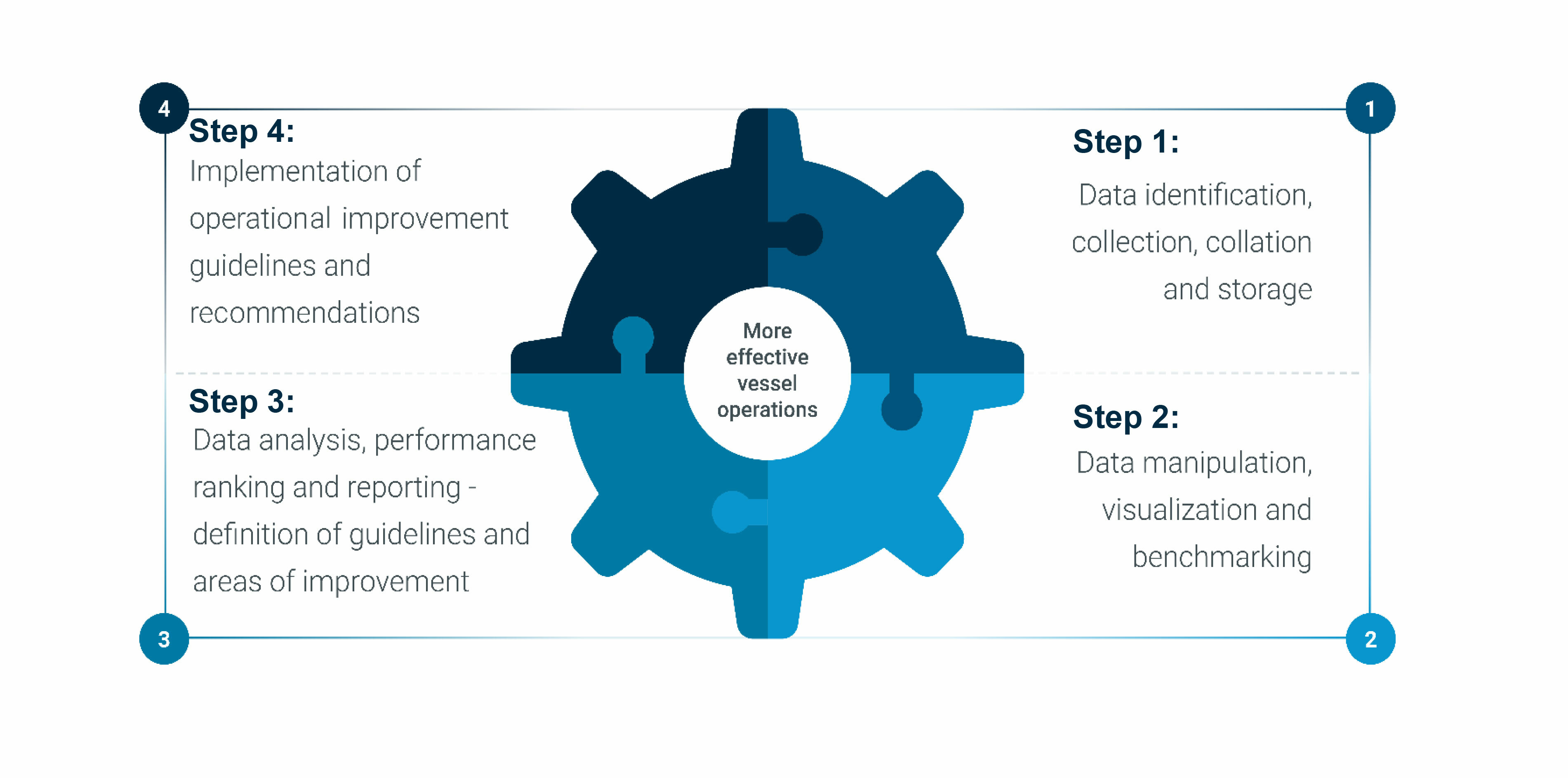
Step 1: Data identification, collection, collation and storage
Selecting the right data inputs is essential for a successful digital strategy. In a preceding article, we have suggested our four-step approach for selecting and effectively identifying the right data signals.
BlueBox smartly enables data retrieval and storage. Due to its flexible configuration, it enables its integration in “almost” any vessel and allows the collection of data from multiple systems onboard according to the needs of the digital strategy.
Step 2: Data treatment, visualization, and benchmarking
Data visualization is the first stage of analysis, interpretation, and display of data. Time series-based data visualization can be important for real-time decision-making, both onshore and offshore, but also for a better understanding and study of past operations to improve for the future. Grafana or X-Connect Studio are good platforms to start monitoring your vessel operations.
Step 3: Data analytics, performance ranking and continual work improvement
Visualization of data is not enough to understand the causes and effects – consequences and implications of individual factors relating to the performance of the vessel. To be able to understand the effect of design, operational and commercial decisions in the overall operating performance of the vessel, we need to rely on fact-based analytics of their operations and the behaviour of the people onboard.
Analyses are carried out by combining data experts, ship designers and people with experience operating the vessels. This combination ensures that results are interpreted correctly, and contextual factors not registered in the data (operational practices, crew shifts, operational requirements, etc) are considered.
As of now, Ulstein offers a set of modular analytics services as defined below:
- SM1. System logistics, routing, and operational profile management
- SM2. Speed utilization
- SM3. Seakeeping performance, operability, and sea-sickness profile of the vessel
- SM4. Fuel consumption analyses benchmarking and performance ranking
- SM4.1. Dynamic environmental indexing (EEOI, etc)
- SM5. Energy management (power plant utilization)
- SM6. Trim & propulsion performance analysis
- SM7A. Crew behaviour and operational performance (based on data facilitated and provided by the owner)
- SM7B. Crew behaviour and operational performance (based on data captured from a field study including stay on board)
Step 4: Implementation of operational improvement guidelines and recommendations
The last stage in the process towards more effective ship operations, but not least important, is the implementation of corrective actions and follow-up. Once performance improvements have been identified and corrective actions proposed, the operators and crew should be prepared to carry them out and live by them accordingly. This can be performed based on training workshops with operators and other relevant personnel, or onboard or web-based field studies including training sessions.
Eager to learn more? Let’s get in touch and talk more about how digitalization possibilities can improve the effectiveness of your vessel operations.
Please contact us for more information
