Simplified shipbuilding
When presenting the X-BOW® design in 2005, the designers claimed that these vessels would be easier and less resource intensive to build. In 2006, this statement was tested in reality through the construction of an X-BOW® hull at Maritim Ltd: "It was easier to build the backward-sloping bow than a conventional bow."
‘We were excited before we started, but the construction work went very well when building an X-BOW hull’, said the manager of Ulstein Poland at the time, Anders Sundgot. ‘It was actually easier to build these hulls with a backward sloping bow than a conventional bow. The lines are more clear on a traditional hull. The traditional bow has a bulb, which is built-in on an X-BOW® vessel. This means that we did not have to use that many double-curved plates. It was a lot easier to build the hull, and I am therefore not in doubt to claim that we saved a lot of production hours on this hull’.
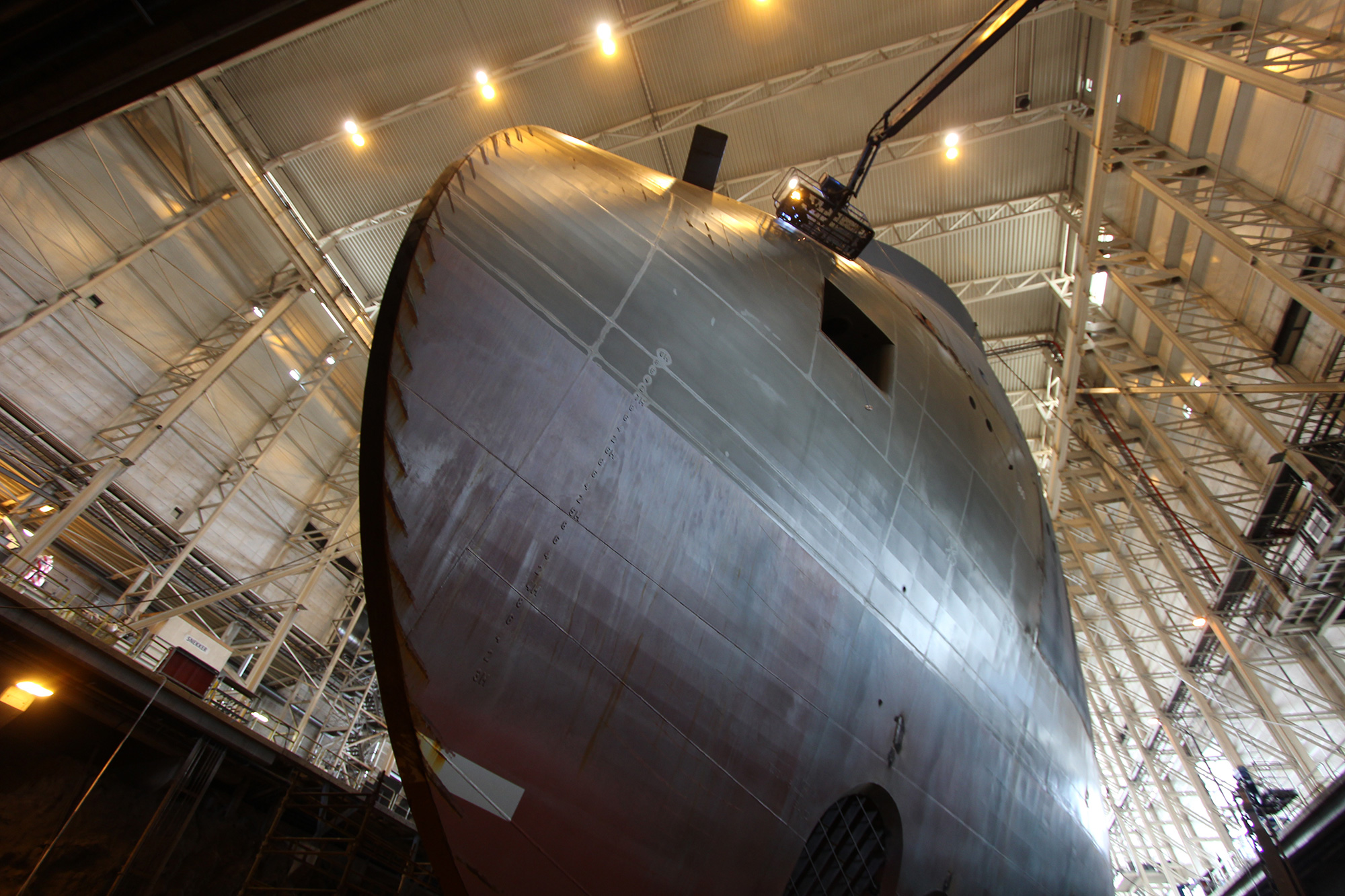
When Zaliv shipyard in Ukraine was commissioned to build their first X-BOW® hull in 2007, they were therefore asked to look more closely into the savings when building the X-BOW® hull compared to other conventional hulls. Marketing Director Yuriy Dovgiy concluded the following positive results in a letter to Ulstein Verft´s managing director in 2009:
- The Labour inputs for producing of relative parts and section were reduced by 15% in comparison with conventional bulb-bows of other projects.
- The Costs for assembly / welding and bending rigging were half as less as for the conventional bow, because a large number of bending templates as well a lot of checking and marking works were not necessary.
- The possibility of wide application of advanced methods of assembly and welding, namely "frame" method of production, automatic welding of several connections and subsections, semiautomatic flux-cored welding on ceramic base.
- The Reduction by 15% of adjustment and fitting works when aligning in the dock during forming of the hull owing to simplification of the form of the outer shell butt joints.